De coatingmethoden van fotoresist worden over het algemeen onderverdeeld in spincoating, dompelcoating en rolcoating, waarvan spincoating het meest wordt gebruikt. Door middel van spincoating wordt fotoresist op het substraat gedruppeld en kan het substraat met hoge snelheid worden geroteerd om een fotoresistfilm te verkrijgen. Daarna kan een vaste film worden verkregen door deze op een hete plaat te verwarmen. Spincoating is geschikt voor het coaten van ultradunne films (ongeveer 20 nm) tot dikke films van ongeveer 100 µm. De kenmerken ervan zijn een goede uniformiteit, een uniforme filmdikte tussen de wafels, weinig defecten, enz., en er kan een film met hoge coatingprestaties worden verkregen.
Spin-coatingproces
Tijdens het spincoaten bepaalt de hoofdrotatiesnelheid van het substraat de filmdikte van de fotoresist. De relatie tussen de rotatiesnelheid en de filmdikte is als volgt:
Spin=kTn
In de formule is Spin de rotatiesnelheid; T is de filmdikte; k en n zijn constanten.
Factoren die het spincoatingproces beïnvloeden
Hoewel de filmdikte wordt bepaald door de hoofdrotatiesnelheid, houdt deze ook verband met kamertemperatuur, vochtigheid, fotoresistviscositeit en fotoresisttype. Een vergelijking van verschillende soorten fotolakcoatingcurven wordt getoond in Figuur 1.
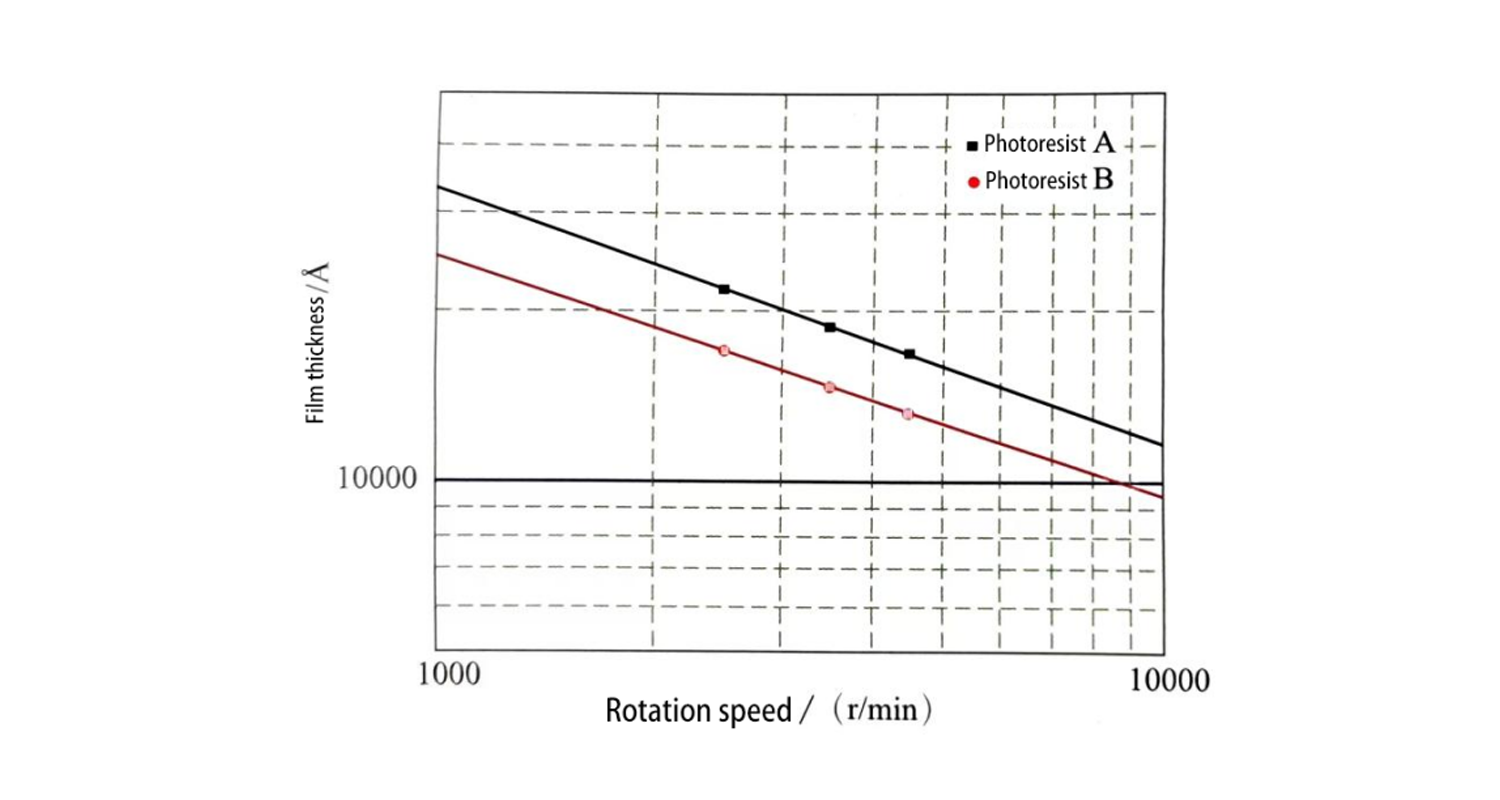
Figuur 1: Vergelijking van verschillende soorten fotolakcoatingcurven
De invloed van de hoofdrotatietijd
Hoe korter de hoofdrotatietijd, hoe dikker de filmdikte. Wanneer de hoofdrotatietijd wordt vergroot, wordt de film dunner. Wanneer deze de 20s overschrijdt, blijft de filmdikte vrijwel onveranderd. Daarom wordt de hoofdrotatietijd doorgaans op meer dan 20 seconden gekozen. De relatie tussen de hoofdrotatietijd en de filmdikte wordt getoond in Figuur 2.
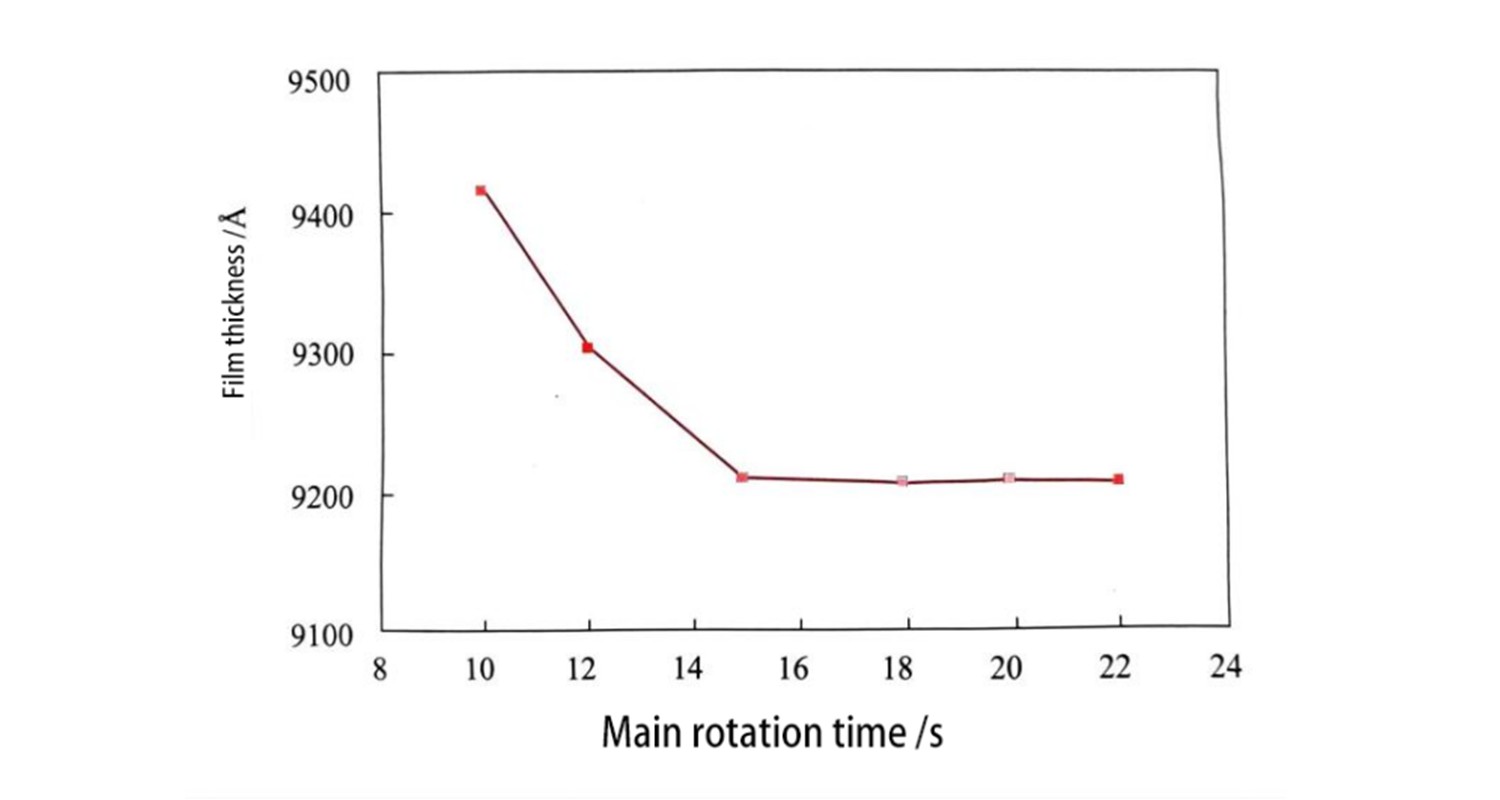
Figuur 2: Relatie tussen hoofdrotatietijd en filmdikte
Wanneer de fotoresist op het substraat wordt gedruppeld, zelfs als de daaropvolgende hoofdrotatiesnelheid hetzelfde is, zal de rotatiesnelheid van het substraat tijdens het druppelen de uiteindelijke filmdikte beïnvloeden. De dikte van de fotoresistfilm neemt toe met de toename van de rotatiesnelheid van het substraat tijdens het druppelen, wat te wijten is aan de invloed van de verdamping van het oplosmiddel wanneer de fotoresist na het druppelen wordt uitgevouwen. Figuur 3 toont de relatie tussen de filmdikte en de hoofdrotatiesnelheid bij verschillende substraatrotatiesnelheden tijdens het druppelen van de fotolak. Uit de figuur blijkt dat met de toename van de rotatiesnelheid van het druipende substraat de filmdikte sneller verandert, en dat het verschil duidelijker is in het gebied met een lagere hoofdrotatiesnelheid.
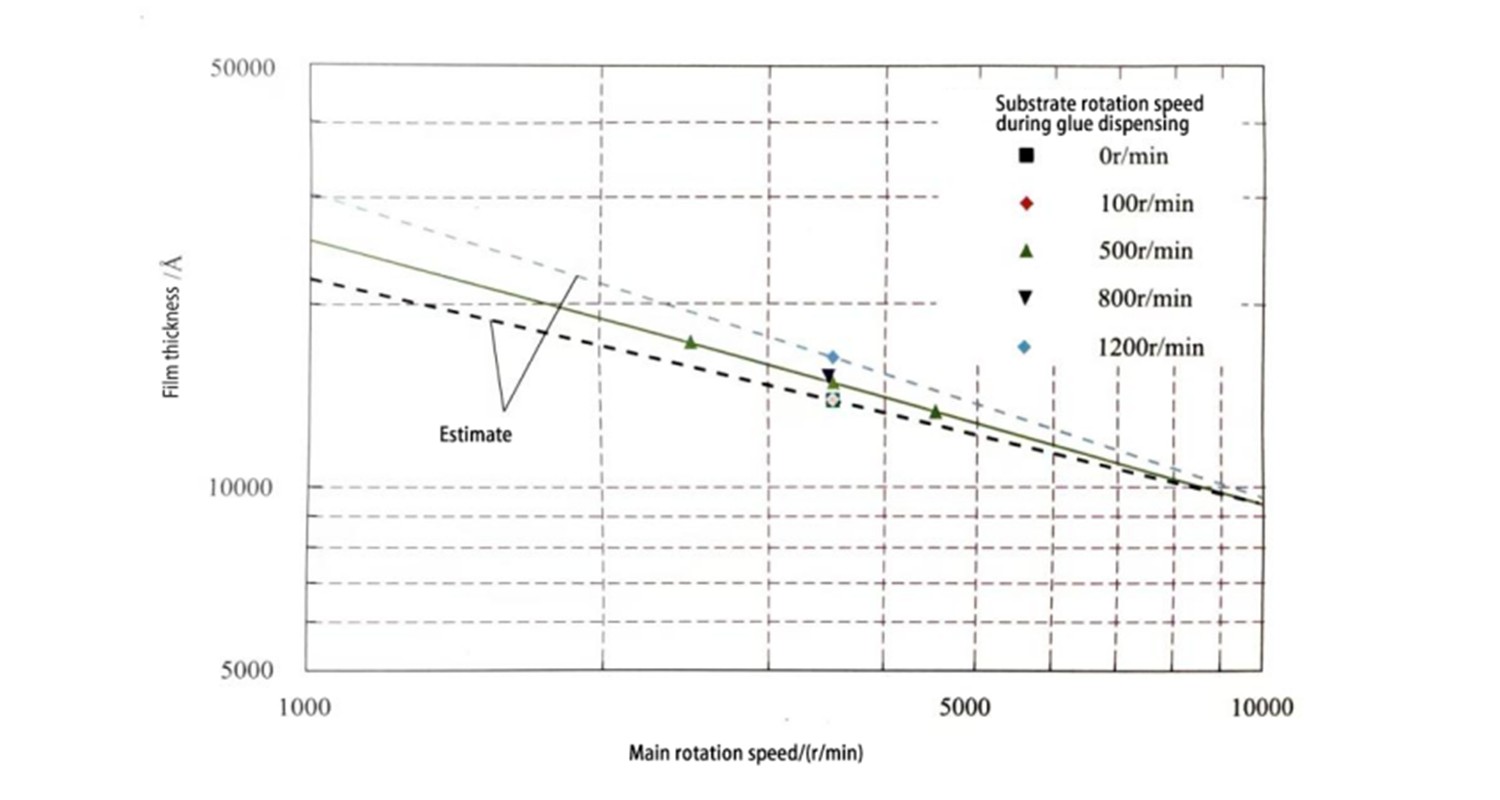
Figuur 3: Relatie tussen filmdikte en hoofdrotatiesnelheid bij verschillende substraatrotatiesnelheden tijdens het doseren van fotoresist
Effect van vochtigheid tijdens het coaten
Wanneer de luchtvochtigheid afneemt, neemt de filmdikte toe, omdat de afname van de luchtvochtigheid de verdamping van het oplosmiddel bevordert. De filmdikteverdeling verandert echter niet significant. Figuur 4 toont de relatie tussen vochtigheid en filmdikteverdeling tijdens het coaten.
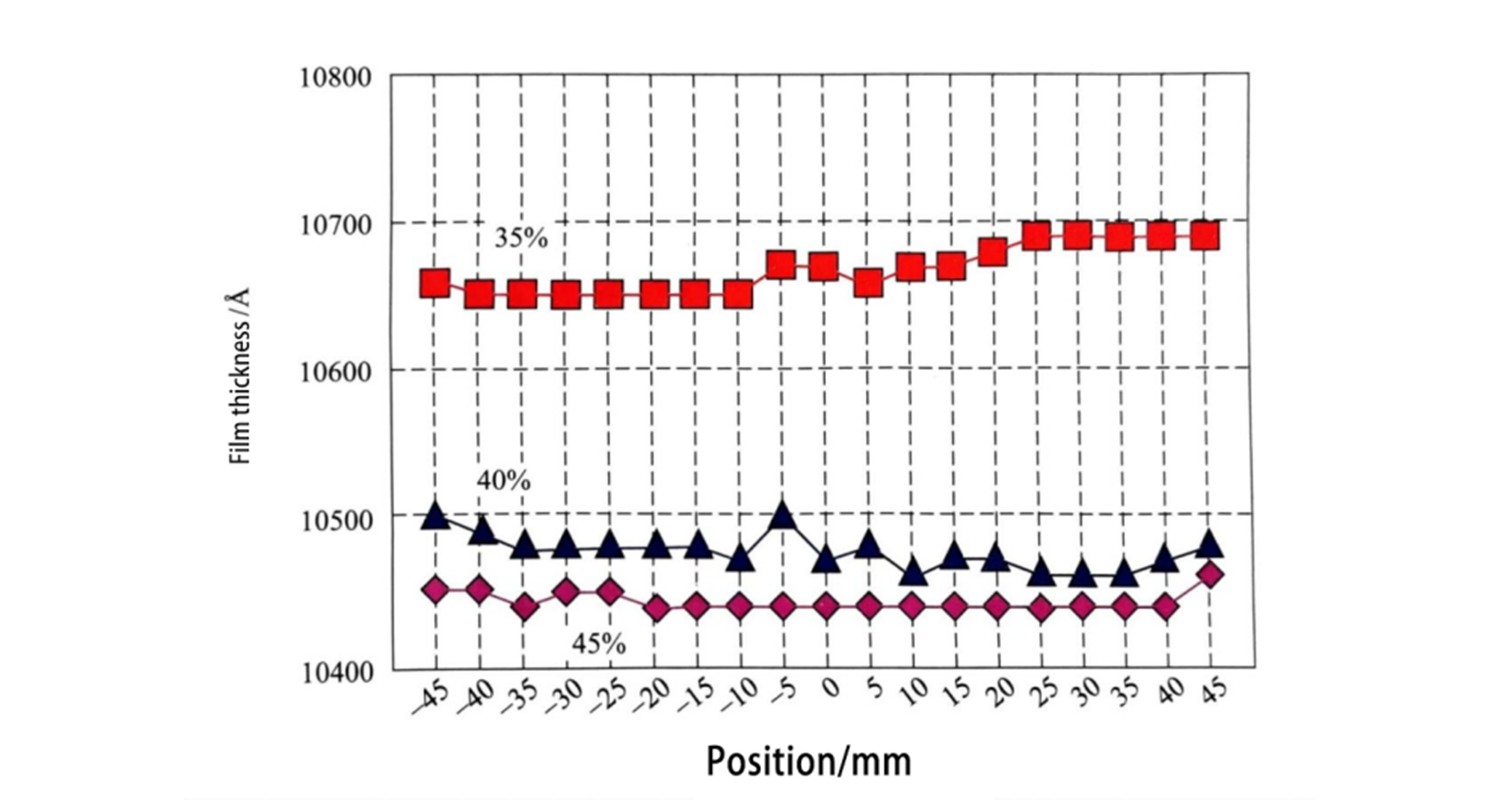
Figuur 4: Relatie tussen vochtigheid en laagdikteverdeling tijdens het coaten
Effect van temperatuur tijdens het coaten
Wanneer de binnentemperatuur stijgt, neemt de filmdikte toe. Uit Figuur 5 blijkt dat de dikteverdeling van de fotoresistfilm verandert van convex naar concaaf. De curve in de figuur laat ook zien dat de hoogste uniformiteit wordt verkregen wanneer de binnentemperatuur 26°C is en de fotoresisttemperatuur 21°C.
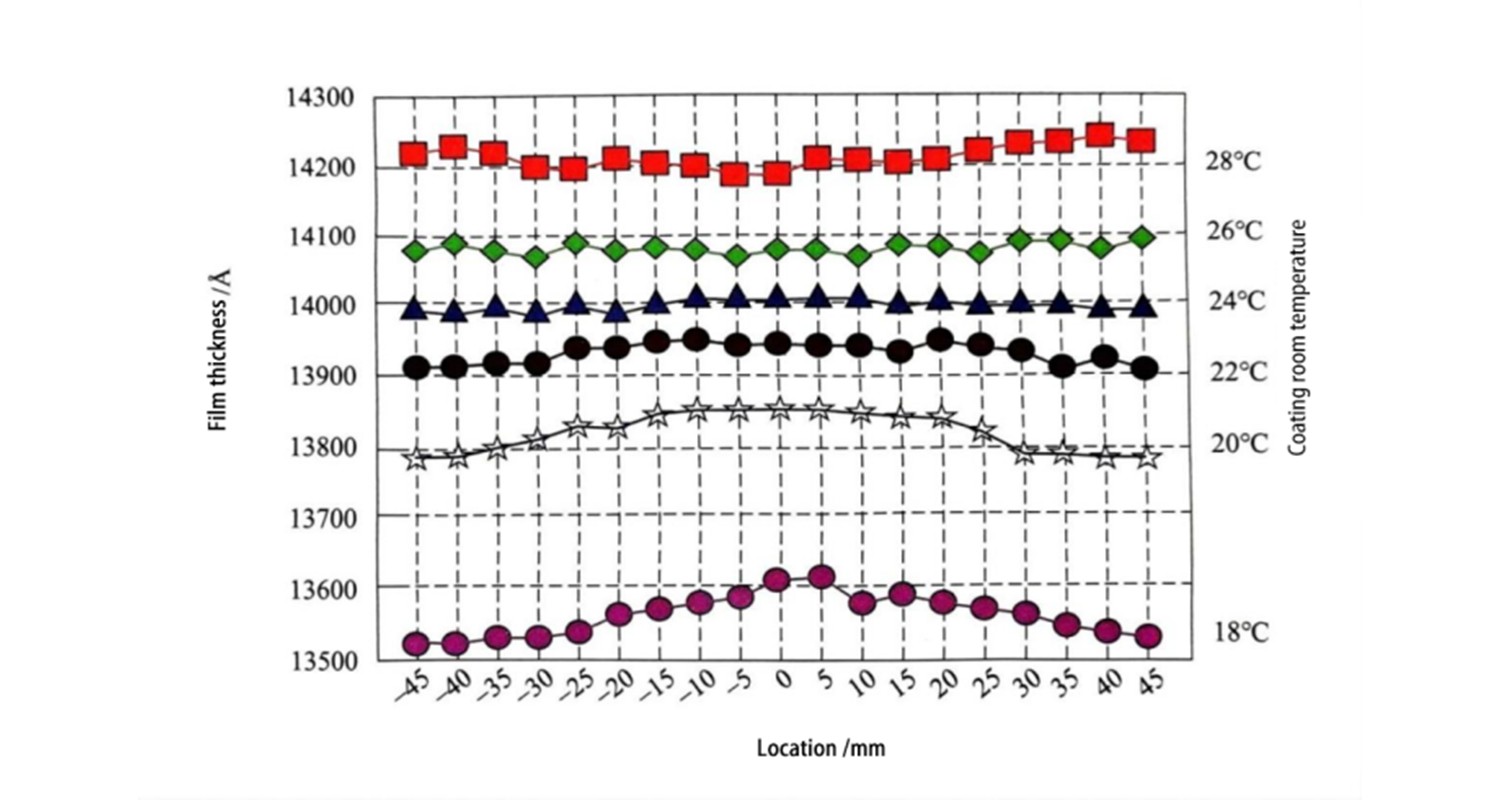
Figuur 5: Relatie tussen temperatuur en laagdikteverdeling tijdens het coaten
Effect van uitlaatsnelheid tijdens coating
Figuur 6 toont de relatie tussen de uitlaatsnelheid en de filmdikteverdeling. Bij afwezigheid van uitlaatgassen blijkt dat het midden van de wafel de neiging heeft dikker te worden. Het verhogen van de uitlaatsnelheid zal de uniformiteit verbeteren, maar als deze te veel wordt verhoogd, zal de uniformiteit afnemen. Het blijkt dat er een optimale waarde bestaat voor de uitlaatsnelheid.
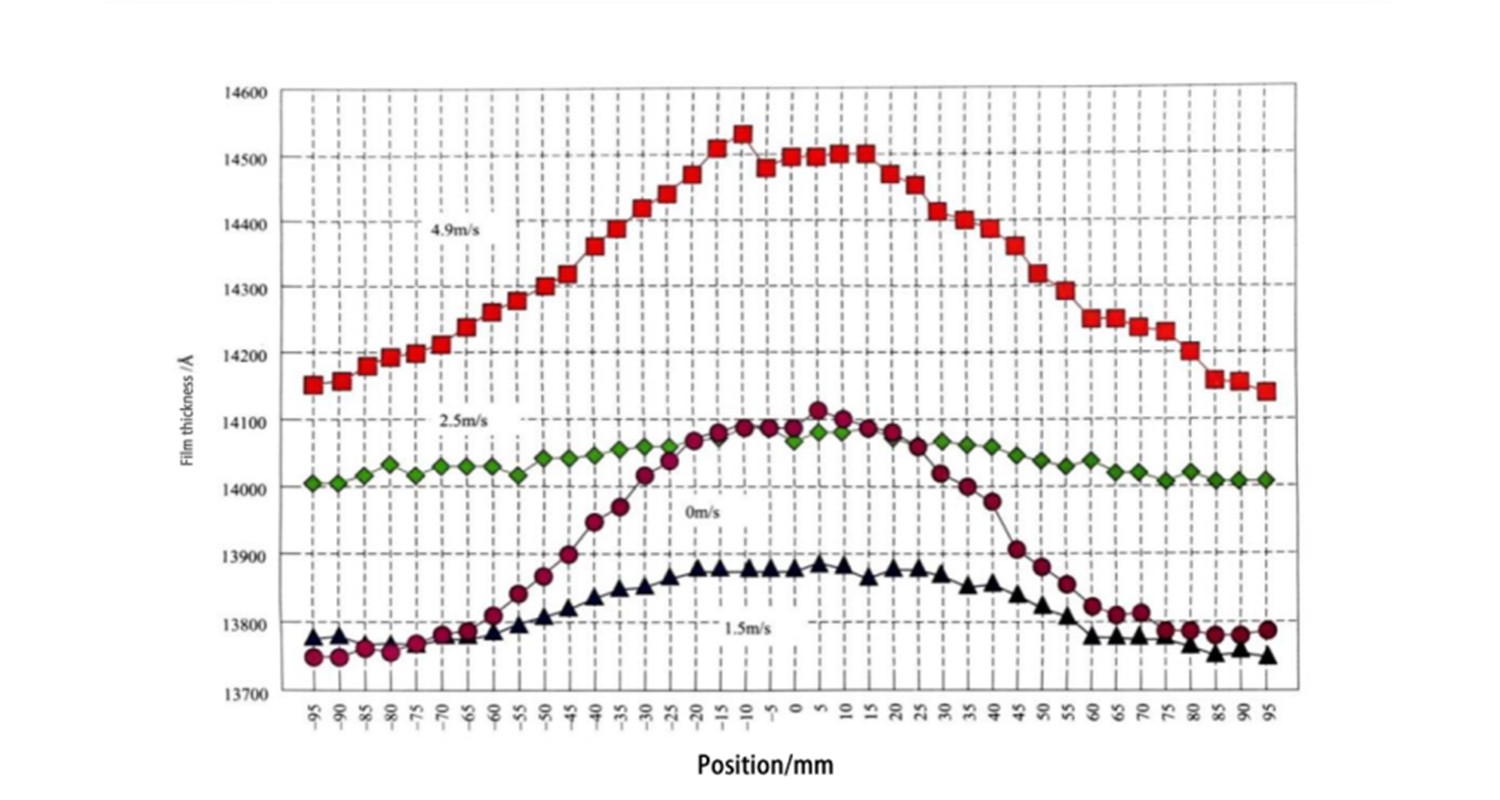
Figuur 6: Relatie tussen uitlaatsnelheid en filmdikteverdeling
HMDS-behandeling
Om de fotoresist beter coatbaar te maken, moet de wafer worden behandeld met hexamethyldisilazaan (HMDS). Vooral wanneer vocht zich aan het oppervlak van de Si-oxidefilm hecht, wordt silanol gevormd, wat de hechting van de fotoresist vermindert. Om vocht te verwijderen en silanol af te breken, wordt de wafel gewoonlijk verwarmd tot 100-120°C, en wordt er mist HMDS geïntroduceerd om een chemische reactie te veroorzaken. Het reactiemechanisme wordt getoond in Figuur 7. Door HMDS-behandeling wordt het hydrofiele oppervlak met een kleine contacthoek een hydrofoob oppervlak met een grote contacthoek. Door de wafel te verwarmen kan een hogere fotoresisthechting worden verkregen.
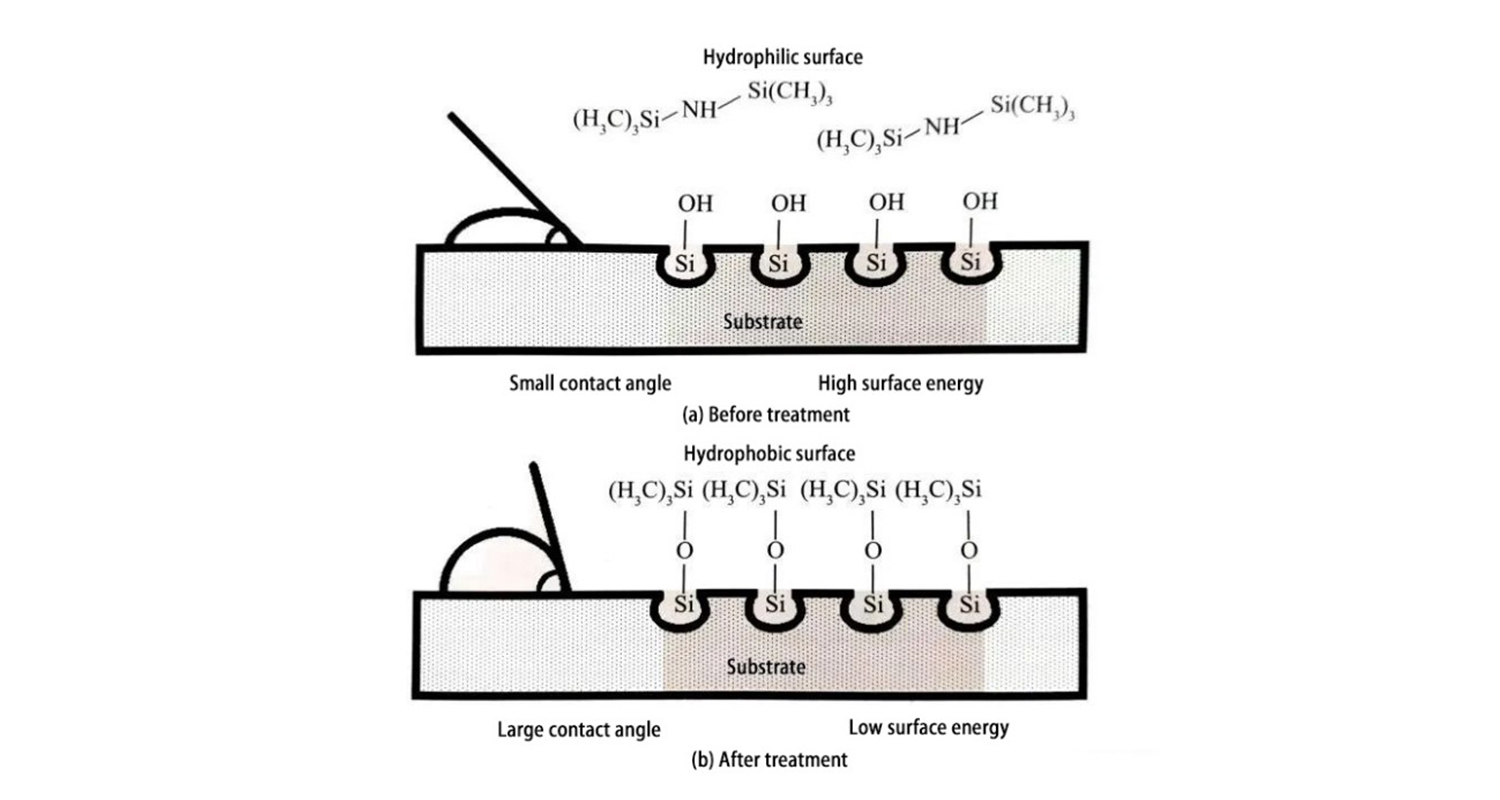
Figuur 7: HMDS-reactiemechanisme
Het effect van de HMDS-behandeling kan worden waargenomen door de contacthoek te meten. Figuur 8 toont de relatie tussen de HMDS-behandelingstijd en de contacthoek (behandelingstemperatuur 110°C). Het substraat is Si, de HMDS-behandelingstijd is groter dan 1 minuut, de contacthoek is groter dan 80 ° en het behandelingseffect is stabiel. Figuur 9 toont de relatie tussen de HMDS-behandelingstemperatuur en de contacthoek (behandelingstijd 60s). Wanneer de temperatuur 120℃ overschrijdt, neemt de contacthoek af, wat aangeeft dat HMDS door hitte ontleedt. Daarom wordt de HMDS-behandeling meestal uitgevoerd bij 100-110 ℃.
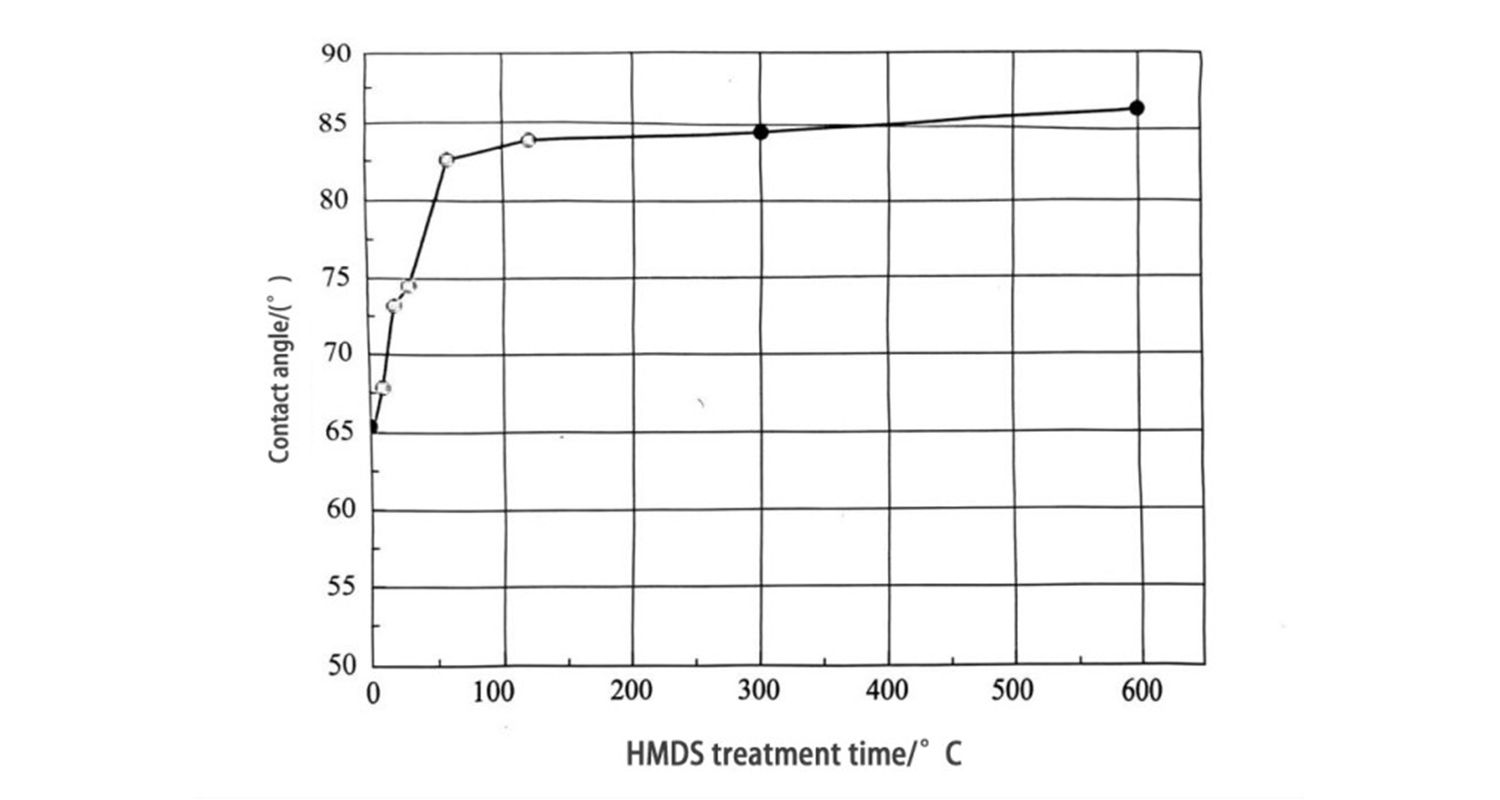
Figuur 8: Relatie tussen HMDS-behandelingstijd
en contacthoek (behandelingstemperatuur 110℃)
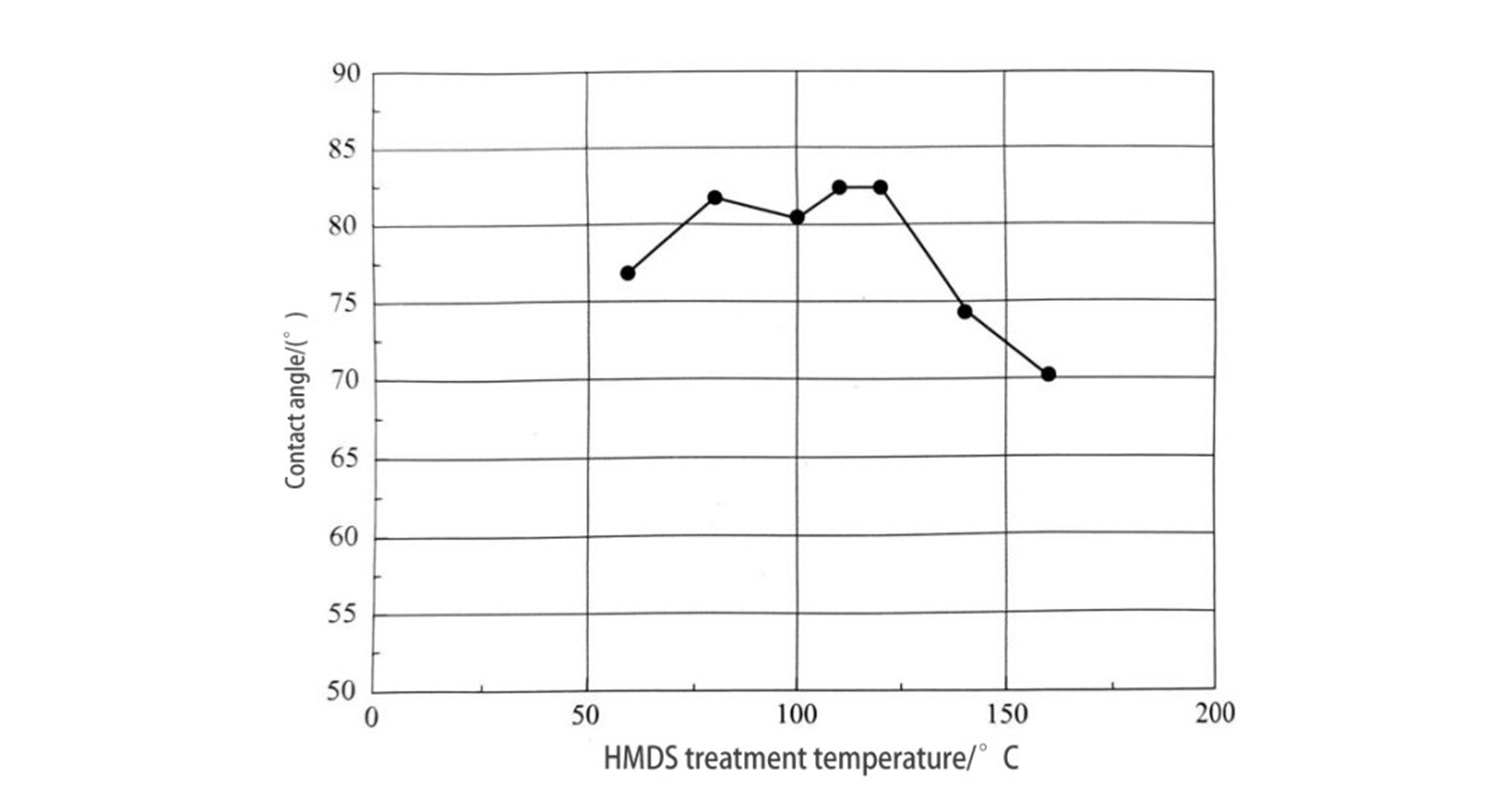
Figuur 9: Relatie tussen HMDS-behandelingstemperatuur en contacthoek (behandelingstijd 60s)
HMDS-behandeling wordt uitgevoerd op een siliciumsubstraat met een oxidefilm om een fotoresistpatroon te vormen. De oxidefilm wordt vervolgens geëtst met fluorwaterstofzuur waaraan een buffer is toegevoegd, en er is gevonden dat na HMDS-behandeling kan worden voorkomen dat het fotoresistpatroon eraf valt. Figuur 10 toont het effect van HMDS-behandeling (patroongrootte is 1 µm).
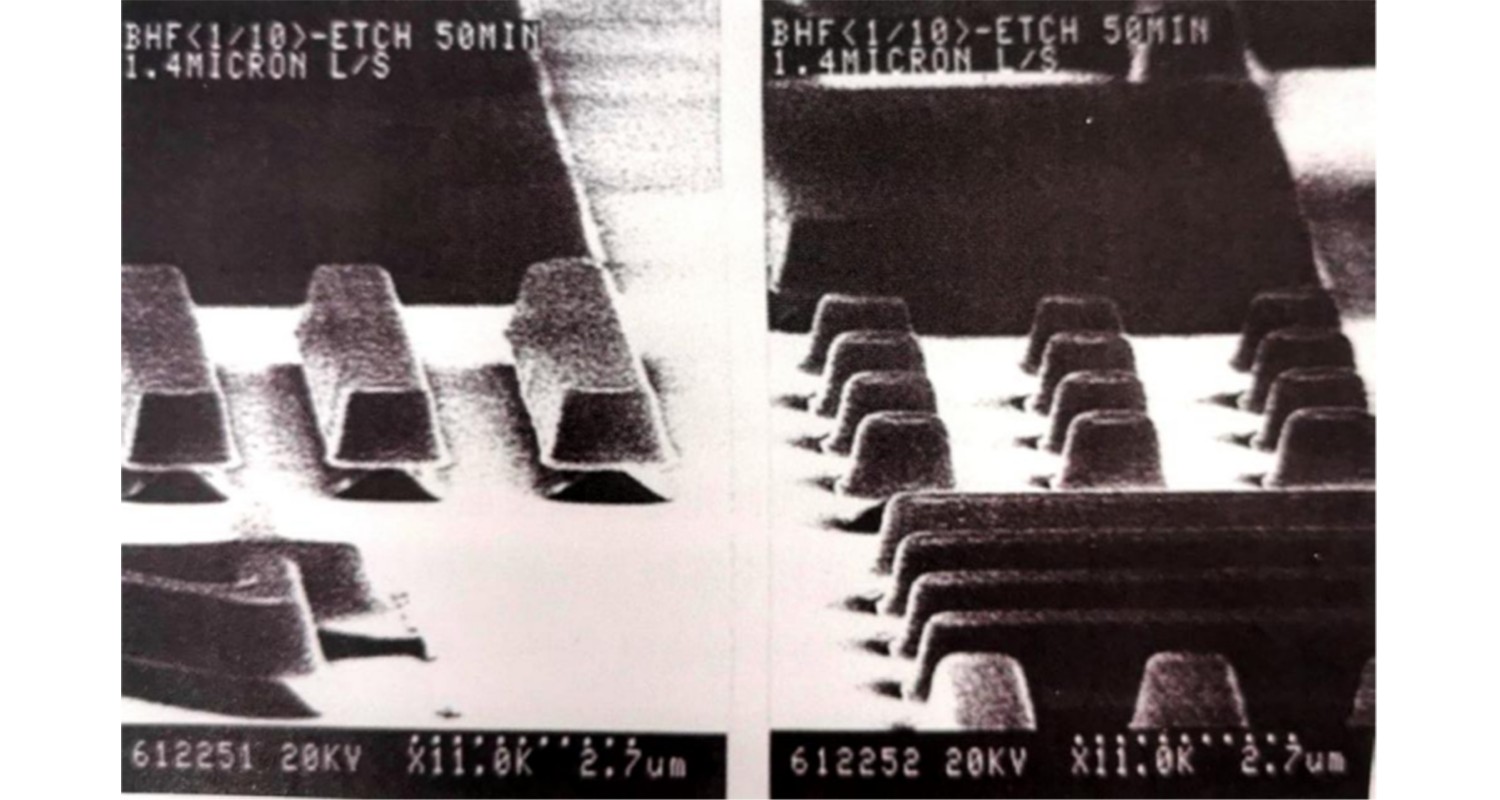
Figuur 10: HMDS-behandelingseffect (patroongrootte is 1um)
Voorbakken
Bij dezelfde rotatiesnelheid geldt: hoe hoger de voorbaktemperatuur, hoe kleiner de filmdikte, wat aangeeft dat hoe hoger de voorbaktemperatuur, hoe meer oplosmiddel verdampt, wat resulteert in een dunnere filmdikte. Figuur 11 toont de relatie tussen de voorbaktemperatuur en de Dill's A-parameter. De A-parameter geeft de concentratie van het lichtgevoelige middel aan. Zoals uit de figuur blijkt, neemt de A-parameter af wanneer de voorbaktemperatuur stijgt tot boven 140°C, wat aangeeft dat het lichtgevoelige middel ontleedt bij een hogere temperatuur. Figuur 12 toont de spectrale transmissie bij verschillende voorbaktemperaturen. Bij 160°C en 180°C kan een toename in transmissie worden waargenomen in het golflengtebereik van 300-500 nm. Dit bevestigt dat het lichtgevoelige middel bij hoge temperaturen wordt gebakken en ontleed. De voorbaktemperatuur heeft een optimale waarde, die wordt bepaald door lichteigenschappen en gevoeligheid.
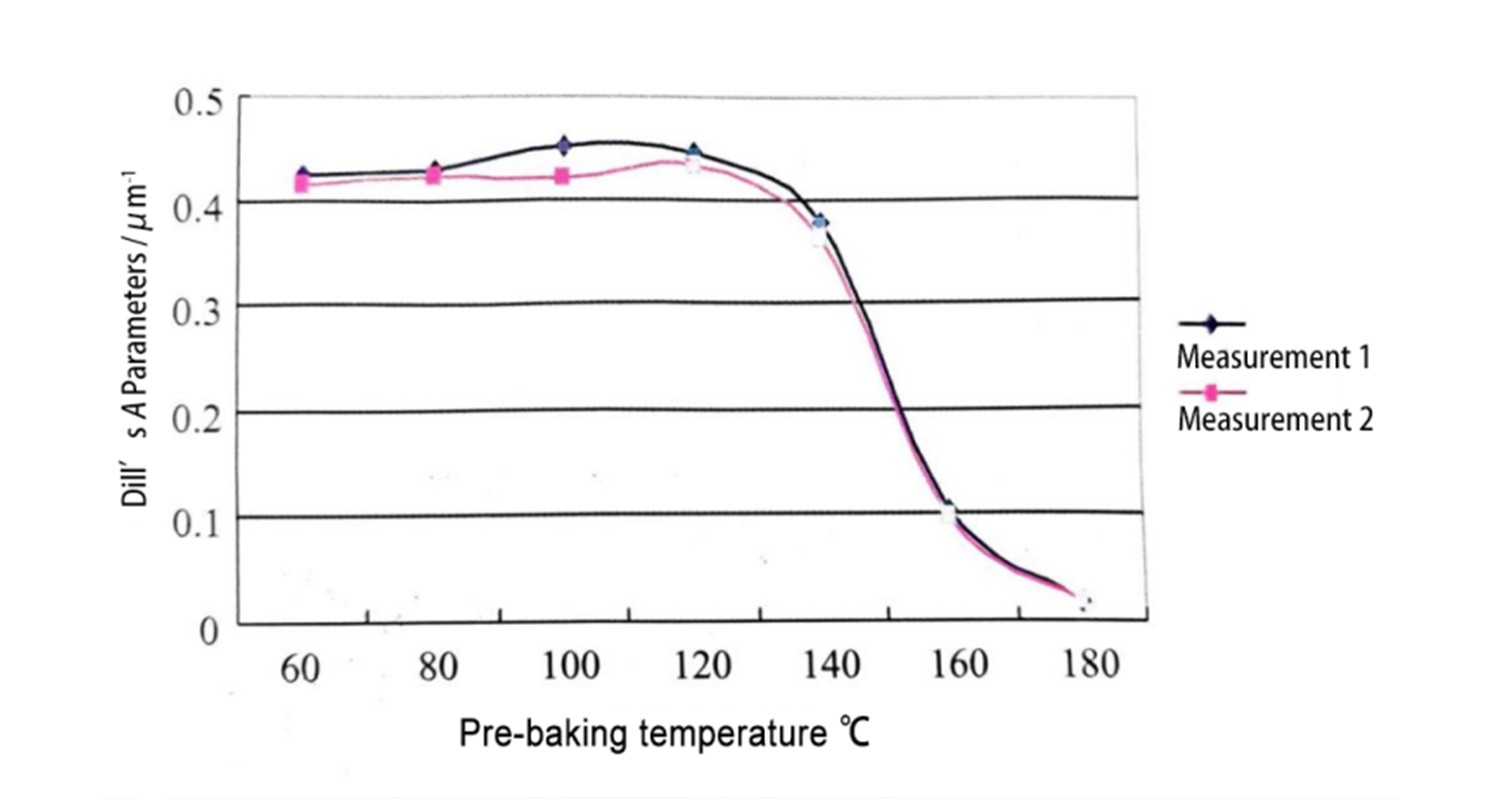
Figuur 11: Relatie tussen de voorbaktemperatuur en de A-parameter van Dill
(gemeten waarde van OFPR-800/2)
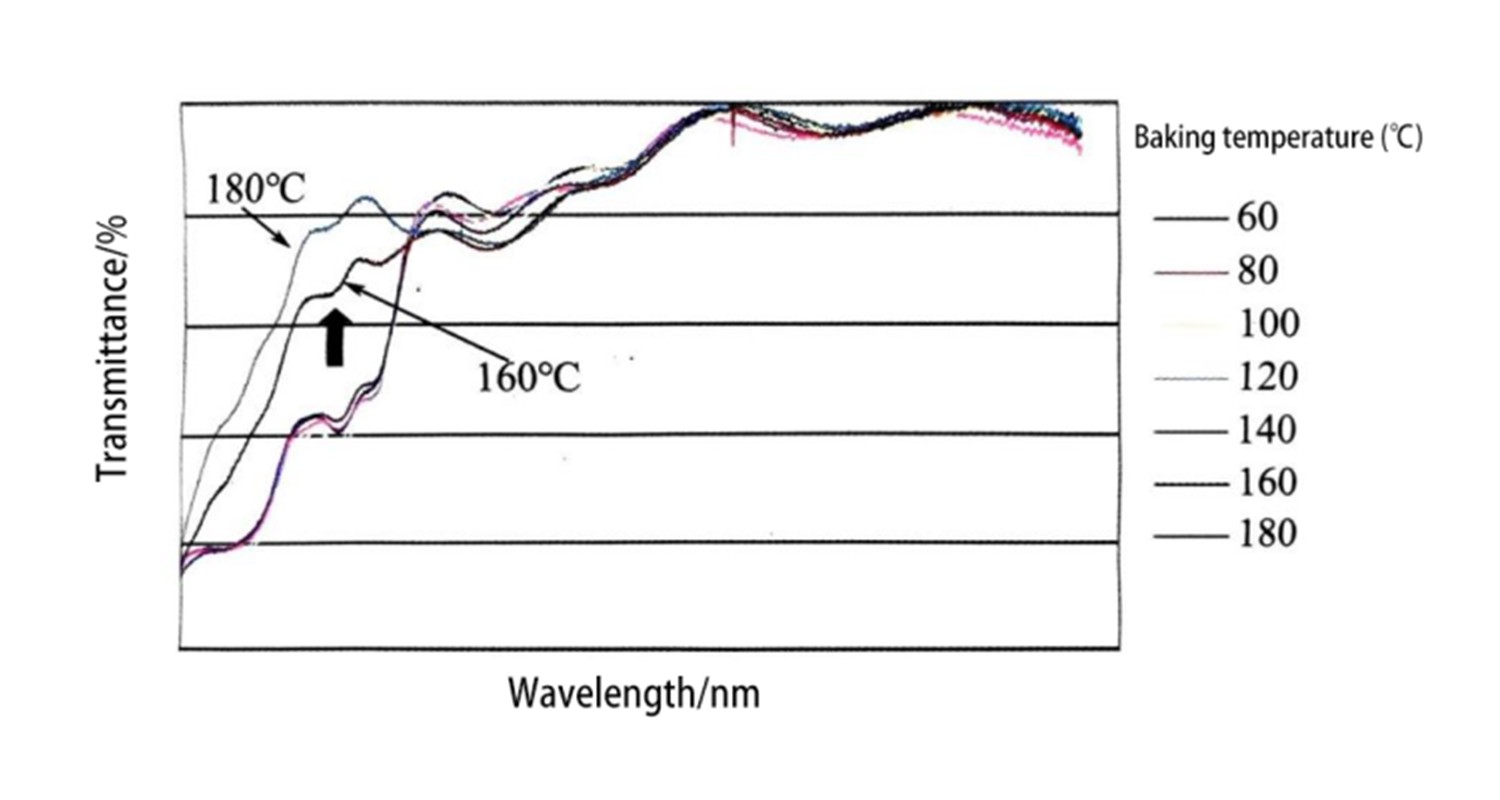
Figuur 12: Spectrale transmissie bij verschillende voorbaktemperaturen
(OFPR-800, 1um filmdikte)
Kortom, de spincoatingmethode heeft unieke voordelen, zoals nauwkeurige controle van de filmdikte, hoge kostenprestaties, milde procesomstandigheden en eenvoudige bediening, dus het heeft aanzienlijke effecten op het verminderen van vervuiling, het besparen van energie en het verbeteren van de kostenprestaties. De laatste jaren krijgt spincoating steeds meer aandacht, en de toepassing ervan heeft zich geleidelijk naar verschillende terreinen verspreid.
Posttijd: 27 november 2024